Gas Monitoring in Enclosed Parking Facilities
Mechanical engineers are usually responsible for designing the ventilation system in enclosed parking garages. The design is based on ASHRAE Standard 62. The standard recommends 0.75 CFM/square foot of floor area for fixed exhaust ventilation. With a typical 8 feet high ceiling, a 20000 square foot garage has 5.6 air changes per hour, which is a large volume of air. The air volume depends on the frequency and number of cars entering and leaving the garage.
When an enclosed parking facility needs a gas monitor, the ventilation system is likely already in place. Therefore, the Contractor selects the quantities required and the types of devices. The gas monitors for parking garages detect Carbon Monoxide (CO) and Nitrogen Dioxide (NO2) gases emitted by vehicles. CO is a colorless, odorless, tasteless, flammable gas that is slightly less dense than air. NO2 is a highly poisonous nonflammable gas.
Ventilation systems are typically designed around the amount of airflow needed for each garage floor. Gas monitors, however, are installed per area covered. Each gas monitor senses the air within a certain radial distance from the device, typically 50 feet. Parking space dimensions range in width and length; the standard size of a parking space in North America is usually around eight feet wide by 16 feet long. Twelve parking spaces 8 feet wide with a pillar in the middle is the sensing area of most gas monitors.
The layout of the gas monitors in a parking garage is typically shown on mechanical drawings by sketching circles for the coverage area of each sensor. Having overlapping circles optimizes the sensor coverage. There are many differing opinions from manufacturers and integrators on the best layout approach. The 50 feet radius method is standard across most manufacturers of gas monitors. There will be pillars spaced around the garage to hold up the ceiling in most cases. Pillars are an excellent mounting location for gas monitors.
Depending on the jurisdiction, the building code may require the gas monitors for CO to be four feet off the floor and NO2 mounted at half the ceiling height. In a typical 8 feet high garage, both could be mounted at the same height. In this case, a dual-sensor gas monitor or two separate gas monitors for CO and NO2 may be appropriate. Selecting a dual-sensor gas monitor reduces labor installation in half.
Some manufacturers rely on centralized systems to control their ventilation systems. Some monitors have relays to perform control functions, and others have network interfaces to a BMS. A central controller for gas monitoring is less necessary when a building employs a Building Management System (BMS). The BMS provides communication, data gathering, and graphical display functions. Most gas monitors offer a BACnet interface or onboard BACnet to connect the systems with little effort.
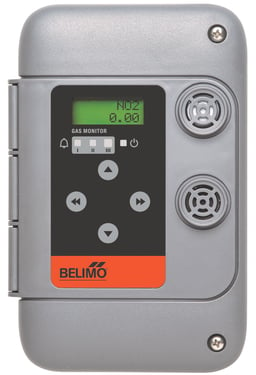
The steps to programming a gas monitor is detailed in the operations manual. A manufacturer-trained integrator can provide valuable input on the control parameters used, such as the thresholds for each gas detection level, which determines when the audible and visual alarms will turn on. Once the system is programmed, commissioning it to ensure everything is working is the final step. In some jurisdictions, occupancy of the space is not allowed until commissioning is completed. In many cases, a factory-trained gas detection integrator must perform this step. The integrator should supply a system verification certificate to prove the system's performance.
Gas monitors assist in removing toxic gases. The demand control function limits fan operation on an as-needed basis, and the position-based damper control saves energy. The energy is in multiple forms; electrical power to run motors on the fans and heating or cooling energy to provide climate control to the space. An innovative distributed control gas monitoring system with dual sensors installed by trained integrators is a cost-effective way to make buildings with enclosed parking facilities both safe and energy-efficient for years!