Trusted Flow Measurement
Published by
Philip Holoch
on
Glycol is commonly used to prevent heat transfer fluids freezing in heating, cooling, and air conditioning systems. It is typically found in systems where pipework is exposed to the exterior environment – rooftop units, free cooling, cooling towers, district cooling systems, and green energy applications, such as solar thermal collectors. Glycol into any system can result in large errors in thermal energy measurement when using a meter intended for water alone.
The solution, Belimo’s technology advanced ultrasonic inline flow sensor that offers automatic, continuous glycol measurement and compensation, ensuring optimal HVAC system performance. Using ultrasonic transit-time technology provides an accurate method for thermal energy measurement that is insensitive to magnetite problems – unlike electromagnetic flow sensors – has a longer lifetime than impeller technology and is suitable for use with a wide range of heat transfer fluids of varying glycol concentrations.
How it Works
The ultrasonic flow meter uses two offset transducers (Figure 1) to determine the flow velocity by measuring the speed of sound in the heat transfer fluid. The downstream transit time is measured by passing an ultrasonic pulse from the lower transducer to the upper transducer, then the process is reversed to obtain the upstream transit time. These transit times will differ based on the flow of fluid through the sensor tube: the downstream pulse is accelerated by the flow, while the upstream pulse is impeded and slowed by it. The transit times of these ultrasound pulses can be used to determine the measured velocity (𝑣𝑚𝑒𝑎𝑠).
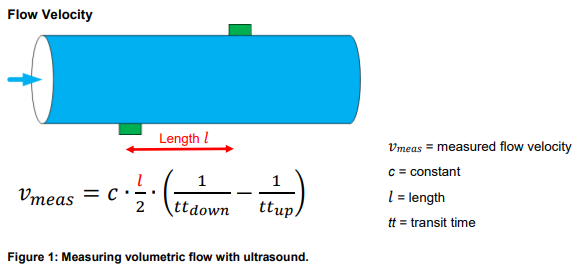
This data, together with the fluid temperature, can then be used to calculate the kinematic velocity (η) and determine the volumetric flow. However, as volumetric flow requires an average of the flow velocities across the diameter of the pipe – not just a single pathway – this is affected by differing flow profiles (Figure 2). In laminar flow (grey), the velocity is greatest in the center and slower at the pipe wall. In contrast, in turbulent flow (blue) the flow velocity is virtually identical across the pipe diameter. This effect is usually compensated for during production by using correction curves to calibrate the flow sensor. However, as the flow profile is influenced by fluid viscosity, the presence of glycol in the system can lead to significant measurement error.
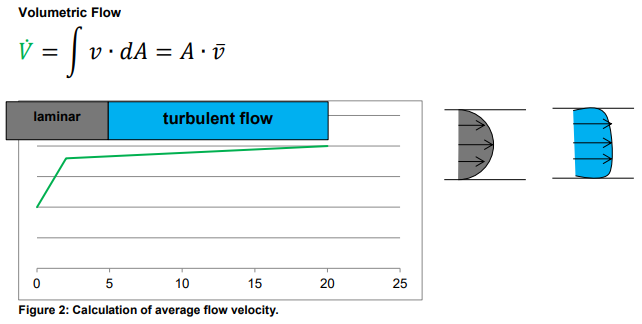
An alternative approach is to use the Reynolds number (Re) rather than the flow velocity. The Reynolds number is the ratio of the inertial forces due to the momentum of the mass of a flowing liquid to its viscous forces:

The practical significance of this ratio is that the flow velocity distribution is similar for a given Reynolds number and geometry. Consequently, the correction factor (k) – used to relate the volumetric flow to the average velocity across the cross-sectional area of the pipe – plotted as a function of Reynolds number is independent of the fluid viscosity, and the resulting water and glycol-water calibration curves superimpose. This means that the sensor can be calibrated with water and still accurately measure any other fluid of known viscosity. The process is summarized in Figure 3.
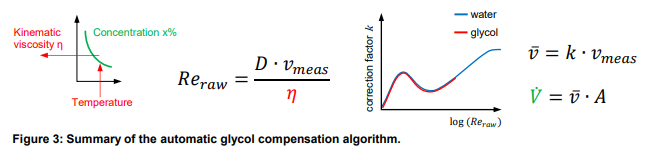
This Reynolds number approach has been used to develop a patented automatic glycol compensation algorithm that is able to select the correct fluid properties to use for the flow and energy calculation, and can be applied to a wide range of heat transfer fluids, ensuring accurate, repeatable measurements in any HVAC application.
Accurate Results Without Drift
The benefit of glycol compensation is clearly demonstrated in Figures 4 and 5. Without compensation (Figure 4), volumetric flow measurements can show errors of as much as 30 percent; the application of automatic glycol concentration (Figure 5) minimizes drift and significantly reduces the degree of measurement error.
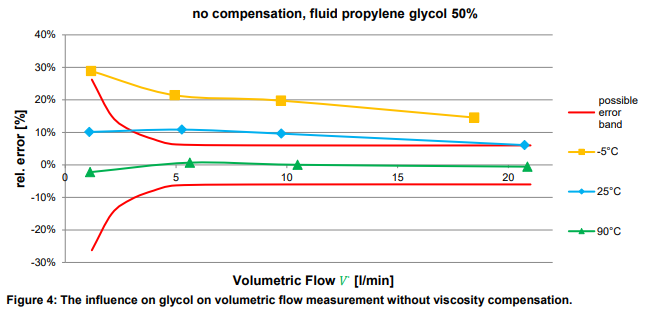
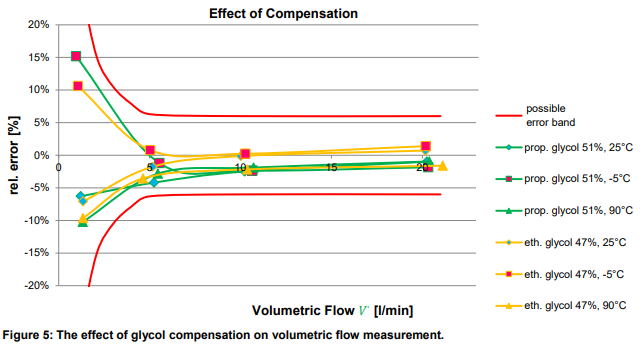
Conclusion
The development of an inline flow sensor that uses ultrasonic transit-time technology to automatically measure and compensate for glycol concentration is a vast advancement in thermal energy measurement. A single ‘fit and forget’ flow sensor is all that is necessary to compensate for the variable and changing viscosities and heat capacities of heat transfer fluids. With no moving parts, the sensor is extremely robust and requires no calibration, providing certainty that the measured flow is correct. This makes it ideal for accurate, repeatable measurements, improving the control and efficiency of HVAC systems.
The development of an inline flow sensor that uses ultrasonic transit-time technology to automatically measure and compensate for glycol concentration is a vast advancement in thermal energy measurement. A single ‘fit and forget’ flow sensor is all that is necessary to compensate for the variable and changing viscosities and heat capacities of heat transfer fluids. With no moving parts, the sensor is extremely robust and requires no calibration, providing certainty that the measured flow is correct. This makes it ideal for accurate, repeatable measurements, improving the control and efficiency of HVAC systems.